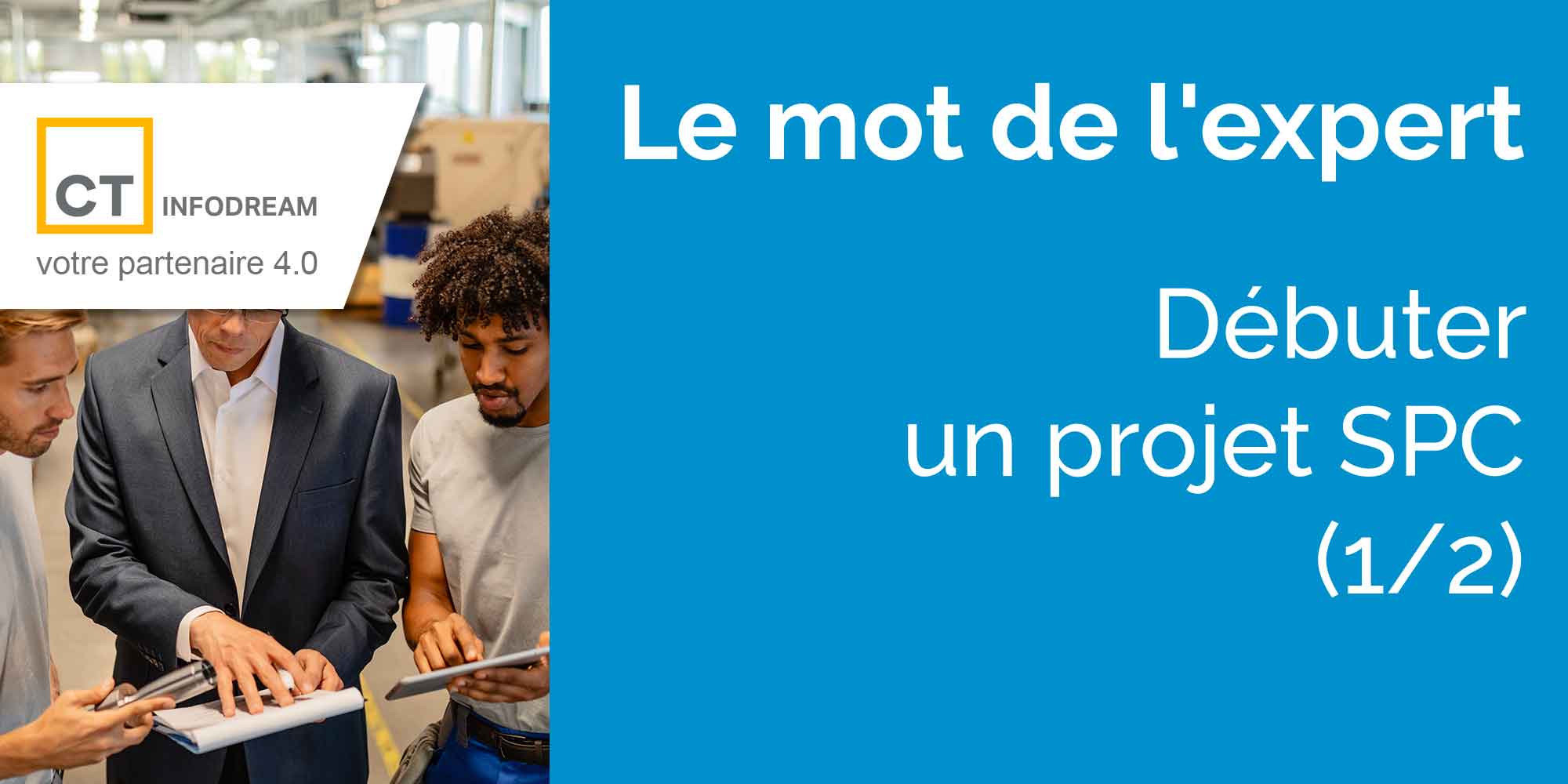
Débuter un projet SPC [1/2]
Lors du démarrage d’un projet SPC dans une société industrielle, certains ingénieurs ou techniciens responsables se sont heurtés à la mauvaise image de marque du « logiciel SPC ».
Certains ont eu de mauvaises expériences avec les cartes papier, d’autres avec un logiciel inadapté ou non ergonomique. Les problématiques suivantes sont parfois évoquées :
- SPC ne fonctionne que pour l’automobile ou la grande série
- Nos règles ne nous permettent pas d’utiliser SPC, nous sommes obligés de faire du contrôle 100%
- Notre volume de production est trop faible
- Nous n’avons pas le temps pour ça
- Nos tolérances sont trop serrées pour le SPC
Cependant, ces mêmes sociétés doivent assumer les coûts d’inspection et de contrôle permanents, les coûts de rebuts, les coûts de rework (réparation, reprise d’usinage…). Nous sommes totalement convaincus qu’il s’agit d’un manque de compréhension de l’ingénierie de la qualité à tous les niveaux de l’entreprise.
Croire que l’inspection finale est la seule façon de garantir sa qualité, tout comme croire que le SPC n’est utile que pour l’automobile est une erreur. Ces idées fausses proviennent d’un manque fondamental de connaissance de la méthode et des outils. Bien que culturellement de nombreux professionnels soient habitués à entendre parler de Cp ou Cpk (capabilité potentielle et réelle du procédé), ils méconnaissent souvent leur utilisation et leur signification correctes. Un procédé est l’ensemble des composantes qui permettent de fabriquer un produit : la Machine, l’opérateur (la Main d’œuvre), les gammes de fabrication / réglage (Méthodes), l’environnement (Milieu), et enfin la Matière (matière première, lot,…). Toute la démarche SPC a pour but d’arriver à maîtriser l’ensemble de ces 5M, donc l’ensemble des causes de variabilité dans la production.
Une bonne illustration peut être la façon de mesurer la performance des processus. Dans de nombreuses entreprises, la « qualité » est fonction uniquement du nombre de rebuts ou de dérogations (le produit n’atteint pas le niveau de qualité prévu, mais il est autorisé à poursuivre dans le flux « normal »). Ce type de mesure ou d’évaluation est uniquement réactif, et bien que fournissant une certaine image de « mauvaise qualité », il ne peut réduire ces coûts de non-qualité de manière proactive.
Il y a un besoin évident de mise en place d’un système surveillant les causes et les effets « de la mauvaise qualité ». Cela inclut un suivi de rendement RFT (Right First Time : Bon du Premier Coup !), suivi des reworks, des dérogations, des capabilités des processus (Cp, Cpk), des alarmes et des tendances visibles dans les cartes SPC. Ce sont ces mesures qui permettent d’identifier vraiment les causes de NQ et finalement d’augmenter la productivité. Sans ce suivi tout au long de la chaine de production, on va souvent se focaliser sur les conséquences des causes assignables plutôt que sur leur détection avant leur élimination.
Si vous envisagez de mettre en œuvre le logiciel SPC, vous devez ou vous allez être pleinement conscients de l’existence de ces questions. C’est un point fondamental, et effacer ces premières attitudes et comportements culturels sera une première étape clé dans la réalisation de votre projet SPC. Il existe ensuite différentes approches de la méthode, mais l’objectif est de veiller à ce que votre premier projet, sur son périmètre pilote soigneusement défini, grand ou petit, soit réussi. Ensuite, les cercles vertueux feront que le déploiement de la méthode s’effectuera naturellement.
Ben Allister
CEO, CT Infodream Ltd (UK)
Lire la suite de cet article : comment débuter un projet SPC 2/2 .